SUPER PROGRAM
Four Sided Planer Moulder Machine SUPER PROGRAM
The SUPER PROGRAM is a wood four sided planer moulder machine that is particularly suitable for industrial woodworking and is also very useful for large-scale joineries that must be able to accommodate high workloads involving large quantities of wood ensuring speed, reliability and safety.
The machine is characterised by the efficiency in the processing of beams, large parquet flooring, coffins, large frames and prismatic and semi-finished products for application in construction.
During woodworking, the SUPER PROGRAM (in all its version) is also suitable, in addition to the operations of wood straightening/planing and profiling, for the moulding of large pieces, thanks to a working width of 350 mm.
The machine is equipped with PLC touch panel for checking the most used axes, allowing enhanced speed both in calibrating settings and passing from one production process to another.
Powerful and versatile with the best technology ever
The SUPER PROGRAM four sided planer moulder machine has been developed to process large woods, for a product quality never seen before thanks to technological solutions created to simplify your daily work.
The structure is solid, with high level components, touch control, rigid structure and linear guides that express the engineering excellence inside in the machine.
Futura Woodmac, always taking care of the quality, develops technologies (such as the drive system) that work to ensure the maximum finishing of the final product.
Technology is at the service of the user, both the wood industry and large-scale carpentries, with a response to every need in order to ensure high performance with maximum precision.
Advantages in Woodworking
- Working width up to 350 mm
- Horizontal counter-supported shafts
- Spindle holder cylinders diameter 120 mm
- Fast, accurate setup when changing tools on the counter-supported shafts
- Adjusting the shafts even while machining
- Touch screen control
- Managing the independent drive system
- Adjustable height of rollers
- Maximum safety (according to the UE)
- Testing and trials prior to delivery
- 100% made in Italy
High performance working units, with maximum precision
Tool holder shafts
Perfect finishing thanks to solidity and sturdiness that characterise the tool holder shafts which ensure accurate, reliable machining even at high speed.
Fitted with 120 mm spindle holder cylinders and bearings able to guarantee 6000 rpm speed standard and 8000 rpm optional.
In addition, a precision centring system is foreseen for quick tool locking.
Machine Performance
The Super Program machine can hold tools with a minimum diameter of 110 mm and maximum diameter of 230 mm.
The vertical shafts’ axis stroke is of 90 mm to machine a higher number of profiles and and allow a rapid work change.
The maximum work sections are of 350 mm in width and of 180 mm in height (200 mm optional).
The minimum work sections are of 25 mm in width and 12 mm in height.
Working units
Each working unit is secured at its base and moves as though it were a single body, thus guaranteeing greater stability while machining.
Working capacity
The Super Program can hold tools with a minimum diameter of 110 mm and a maximum diameter of 230 mm.
The vertical shafts’ axis stroke is of 90 mm to machine a higher number of profiles and and allow a rapid work change.
The maximum standard work sessions are of 350 mm in width and 180 mm in height
Both the shaft strokes and the working capacity can be increased to meet customer requirements.
Counter-supported working shafts
The machine has been designed with horizontal counter-supported shafts to ensure efficiency on high workloads.
The shaft’ sturdiness prevents vibrations and bending in the machined workpiece which could compromise its final quality.
Sturdy structure
Base and Frame
The base and frame are designed to offer strong rigidity to the moulder.
Due to the fact that this is a company with its own metal machining department, we are highly skilled in the production of parts which offer maximum stability and sturdiness to the machinery.
This quality is reflected in the excellent result on the surfaces of the machined workpieces.
Hardox HB400 worktable
The worktable durability is guaranteed by the excellent resilience of Hardox.
This is not a coating but a product already purchased in its entirety which is then welded and machined directly onto the base.
This makes the work surface extremely solid and ensures the pieces can be conveyed easily without friction.
Movement along linear guides and blocks
High quality parts like linear guides and ball runner blocks.
A system that has no fear of wood chips and dust and has a very low noise emission.
Quality control
The mechanical quality control and testing of each manufactured workpiece is an essential part of each order to guarantee top quality and safety standards.
In order to avoid problems and complications at the assembly stage, Metalstar has state-of-the-art machinery with sophisticated size control tools to check every tolerance and critical dimension.
Drive system
Independent drive
To ensure greater solidity on the upper shaft and a total absence of strain, the Super Program machine has an independent drive unit.
Wood feeding
The drive speed is displayed.
Wood feeding is guaranteed by the high number of wheels and by the air cushion system.
The system can be integrated (as an optional) with an air and oil atomisation device.
Air cushion and atomisation system, if combined together, further improve the workpiece handling.
Reduction of the distance between the drive wheels
The optional tandem device and the second drive wheel located in front of the left spindle moulder – standard on every machine – are devices used to reduce the distance between the rollers.
This makes it possible to work safely even on short workpieces, as well as helping the wood stay on line.
Above all, it is recommended for types of wood more difficult to be machined.
Feeding without production downtimes
Infeed wheels and air film to convey the piece.
The film cushion consists of 4 rows of holes that can be individually activated by the operator, as required.
The system can be integrated (optional) with the air and oil atomisation, making it even easier to convey the wood.
Gearboxes with cardan-shaft drive
Feeding unit consisting of oil-bath gear boxes with cardan-shaft drive.
Highly resistant, long-lasting and maintenance-free solutions.
Technology at the user’s disposal
The advantages of the Electronic Control
Super Program is supplied with a state-of-the-art technology.
It comes complete with 7 inches colour Touch screen, and 10 or 15 inches, on request.
Easy and fast to program, it saves setup time thus reducing the risk of error.
The software controls the main working units and the drive unit which is separate from the upper shaft.
It also offers the opportunity to increase the number of controlled axes and customise the operator interface.
Mobile console
The new control panel design makes the machine perfectly ergonomic, making the operator’s daily tasks easier.
Customisation
Customised software
Customised software capable of increasing efficiency and output continuity, making the operator’s everyday work easier.
Controlling the milling cutter’s diameter via PLC
PLC controlled quick setting change of milling cutter diameter on right and left spindle moulders.
This system is suitable for a manufacturing company with a continual change of orders and is ideal even for industrial sectors that customize the production.
Feeding unit on infeed worktable
Designed for big industries, it enables machining on high-output automatic lines.
The system places the wood against the inlet guide, thus ensuring consistency in performance quality.
Left spindle moulder axial stroke
Increased left spindle moulder axial stroke up to 120 mm to allow for the housing of a significant number of tools and, as a result, their rapid positioning via the suitable control.
Data | Value |
---|---|
Max working width (with 125mm/140mm diam. Tools) | 350 mm |
Min. Working width (with 125mm/140mm diam. Tools) | 25 mm |
Max working height (with 125 mm/140 mm diam.Tools) | 180 mm |
Min. Working height (with 125mm/140mm diam. Tools) | 12 mm |
Minimum working length of a single piece | 550 mm |
Feed speed with inverter | 4-30 m/min |
Shaft rotation speed | 6000 rpm |
Vertical-horizontal shafts diameter | ø 40 mm |
Length of infeed worktable | 2500 mm |
1st and 4th unit motor power supply | hp20 – kw 15 |
Vertical spindle moulder motor power supply | hp12 – kw 9 |
Upper/lower 2nd shaft motor power supply | hp12 – kw 9 |
Universal shaft motor power supply | hp10 – kw 7,5 |
Y/d automatic start-up | standard |
Vertical shaft axis adjustment | -90 mm |
1st unit tool diameter | ø 125/140 mm |
Min and max tool diameters (excluding 1st unit and universal) | ø 110/230 mm |
Min and max tool diameters on universal shaft | ø 110/200 mm |
Horizontal counter-supported shafts | Controlled 6 axis / 7 axis programmer (depending on the model selected) |
Pneumatic pre-planer roller with exclusion from control panel | Pneumatic pressure |
Manual lubrication of the worktable | Gearbox drive |
Manual lubrication of the vertical spindle moulders | Hardox HB400 worktable |
Manual lubrication of the guides | Drive shaft extensions for left spindle moulder complete with 45 mm toothed roller |
Air-cushion worktable | Each tool holder shaft is equipped with an independent motor |
Poly-V belt drive system on every tool holder shaft guarantee maximum motor power supply performance | Y/D automatic motor start-up |
Automatic lubrication of the worktable | Automatic lubrication of the guides |
Automatic lubrication of the vertical spindle moulders | Automatic device to search for width of the piece |
We work with 30 suppliers
Interested in this product?
Please contact us if you have any questions about our product range, need assistance with choosing the best solution for you
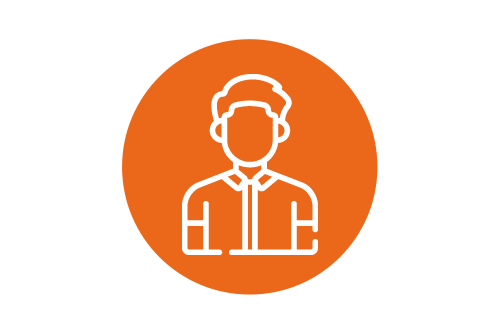
Looking to finance your new machine?
It couldn’t be simpler, thanks to our partnership with Venture Asset Finance. It’s a fast and secure way for your new machine to start generating income!
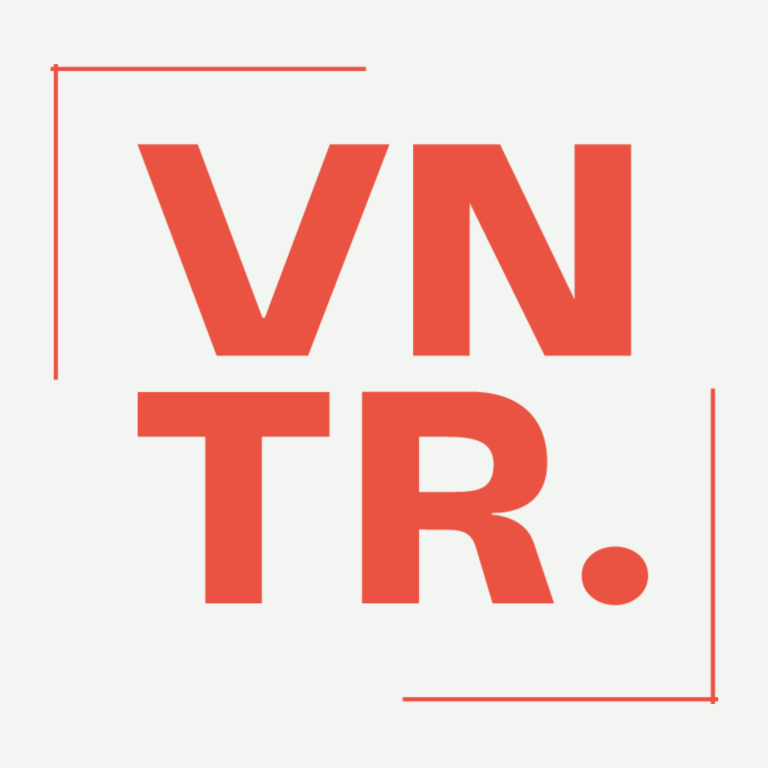