FLS Arrow I
Rip saw with 210mm max cutting height
Maximize your productivity and achieve exceptional cutting results with the FLS Arrow I, Störi Mantel’s flagship single-blade rip saw. Benefit from its unmatched cutting power and a wide array of equipment and mechanization options, creating a tailored solution for optimal efficiency and precision.
Streamline your cutting processes with the FLS Arrow I rip saw. Ideal for medium-sized operations, it efficiently handles various wood and non-wood materials, including prisms, boards, beams, and large-sized pieces. Perform ripping, trimming, crosscutting, shaping, and produce cross-sections and lamellas with ease. This powerful saw, operable by one person, offers a 210mm cutting height (with custom options available).
Safety First
FLS longitudinal cutting technology prioritizes safety at every stage. With comprehensive safety features, operators can confidently position materials, execute cuts, and handle finished pieces without compromising their well-being. This commitment to safety is reflected in the machine’s compliance with rigorous EU regulations and directives.
Basic Equipment with Extraordinary Performance
Even in its basic configuration, the FLS circular saw delivers exceptional results. Smooth blade feed and lift regulation ensure clean cuts and high performance. Blade changes are safe and effortless with the “ProLock” quick-locking system. Guiding and side rollers on the saw carriage provide optimal control during cutting, minimizing vibrations and ensuring a smooth operation.
Precision and Error-Free Operation for Higher Efficiency
FLS technology is designed for intuitive operation and efficient workflows. An ergonomically placed touchscreen panel allows for quick and easy setup. Input cutting widths manually or utilize the “Absolut” basic program, with the option to upgrade to the advanced “Chain” and “Optim” programs. A laser beam precisely guides the sliding saw blade, ensuring millimeter precision for maximum material yield.
Invest only in what you need
You’re in the driver’s seat. Define your requirements, and we’ll deliver. We’ll work with you to understand your material, final product specifications, and desired outcomes. From there, we’ll leverage our comprehensive range of equipment to recommend a solution that not only meets but exceeds your expectations.
Surprising universal application
Designed for demanding applications in furniture making, parquet production, and staircase construction, FLS saws handle a wide range of wood and non-wood materials. Process prisms, beams, boards, and large-sized pieces with ease, whether they have live or straight edges. The saw performs various cuts, including ripping, trimming, formatting, angled cuts, beveling, and grooving, and can produce cross-sections and lamellas. Beyond wood, FLS saws cut materials like PUR/PIR panels, composites, sandwich panels, aluminum, and cement-bonded chipboard.
Rely on innovative solutions
Störi Mantel’s single-blade rip saws are built on a foundation of experience, quality, and innovation, ensuring professional processing and outstanding results. Our saws are crafted with the finest materials and components, empowering you to deliver exceptional product quality that exceeds customer expectations. Invest in reliability and build a brand synonymous with excellence with Störi Mantel.
Optional equipment
Customize your FLS Arrow I rip saw with a range of optional equipment! We’ve listed some popular choices below, but if you don’t see what you need, simply contact us. We’re ready to discuss your unique requirements and help you configure the perfect saw for your application.
Saw
- More powerful motor – the saw can be equipped with a 15 kW, 18.5 kW or 22 kW motor.
- Saw blade of a different diameter – the saw can optionally be fitted with a blade with a diameter of 400-600 mm.
- Smooth saw motor speeds – provided by a frequency converter.
- Movable control panel – the option to move the panel freely along the length of the saw.
- Automatic regulation of cutting resistance
Material handling
- Metal rollers – located between the wooden cross planks on the loading table. They facilitate the movement of material on the table.
- Metal plates with ball bearings – placed between the wooden lining of the machine. They facilitate the movement of material on the table.
- Plastic lining of the cutting area
- Plastic cross planks on the loading table
Cutting conditions
- Second upper pressure – ensures pressure on the material along its entire length. It is suitable from a length of the cut material starting from 4,200 mm.
- Coupled pressure – is always in a parallel position with any length of cut material. It uses a transmission shaft for pressure.
- Length of cut material – can be up to 16,200 mm.
- Width of cut material – can be up to 3,000 mm.
- Second laser
- 3 or 5 quick selection buttons
Material formatting
- Basic cross table (fixed ruler at 90°)
- Additional cross table
Mechanisation
- Bridge stops – suitable in case the saw is used for cross-cutting longer material.
- Chain mechanisation – a device located behind the saw that helps position the material for cutting.
- Clamping stop – additional device for perfect clamping and fixation of the material.
Special equipment
- Heating of the electrical switchboard and control panel – necessary if the machine is located in unheated spaces.
Data | Value |
---|---|
Cut material length | 2 200 – 7 200 mm Option: up to 16 200 mm |
Cut material width | 450 mm Option: up to 3 000 mm |
Maximum cutting height | 210 mm Option: on request |
Cutting height adjustment | electronic – seven-position switch |
Circular saw blade | Ø 400-650 mm |
Blade mounting hole | Ø 80 mm |
Quick-change of the saw blade “ProLock” | ✔ |
Main motor | 11 kW Option: 15 kW, 18,5 kW, 22 kW |
Spindle speed | 2 900 rpm Option: Frequency inverter |
Smoothly adjustable cutting feed | 0 – 80 m/min. |
Table working height | 900 mm |
Minimum extraction speed | 30 m/s |
Extraction connection throat | 2 x Ø 160 mm |
Extraction volume | 4 300 m3/h |
Laser 40mW | ✔ |
Second Laser 40mW | – Option: ✔ |
Thickness of protective slats 8 mm | ✔ |
Material pressure 3,000 mm standard on the left | – Option: ✔ |
Second upper pressure (from cutting length 4,200 mm) | – Option: ✔ |
Coupled material pressure | – Option: ✔ |
Control via 7″ Touchscreen panel | ✔ |
Stop positioning via joystick | ✔ |
ABSOLUT + CHAIN + OPTIM program | ✔ |
Start of cutting – Pedal along the entire length of the machine | ✔ |
Automatic regulation of cutting resistance | – Option: ✔ |
Adjustment of cutting height in 7 positions | ✔ |
Setting the Cutting Length | – Option: ✔ |
Automatic repetition of the cut | – Option: ✔ |
Cross conveyor chains for loading or unloading material | – Option: ✔ |
Ball plates | – Option: ✔ |
Cross table with fixed stop | – Option: ✔ |
Cross table additional | – Option: ✔ |
Mobile cross table | – Option: ✔ |
Temperature control of el. switchboard and control panel | – Option: ✔ |
Electrical voltage/frequency connection | ~3×400 V/50 Hz |
Minimum compressed air supply pressure | 0,6 Mpa |
Air consumption | 30 l/cut |
Maximum air consumption (depending on the number of cuts) | 240 l/min. |
We work with 30 suppliers
Interested in this product?
Please contact us if you have any questions about our product range, need assistance with choosing the best solution for you
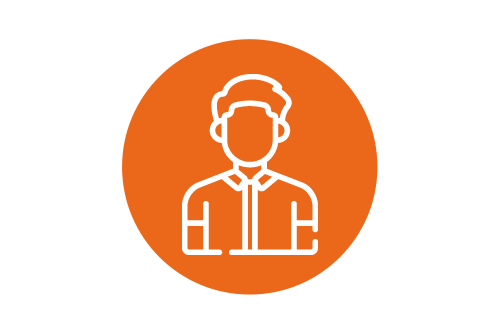
Looking to finance your new machine?
It couldn’t be simpler, thanks to our partnership with Venture Asset Finance. It’s a fast and secure way for your new machine to start generating income!
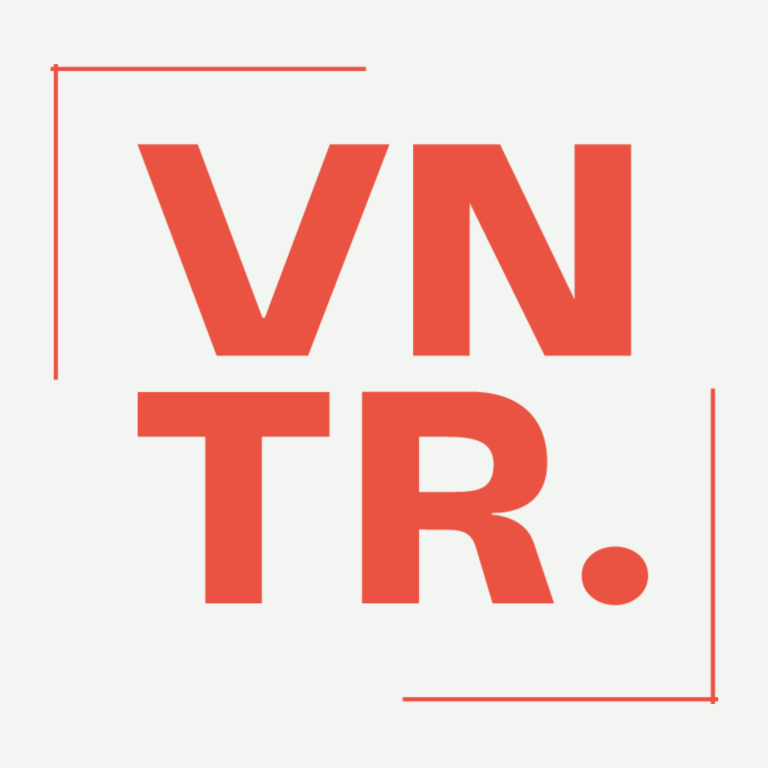